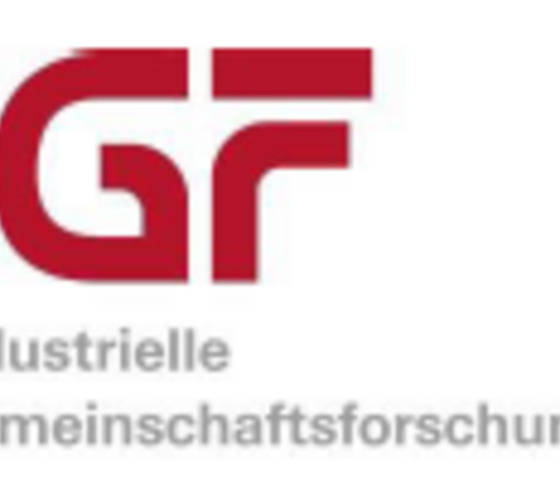
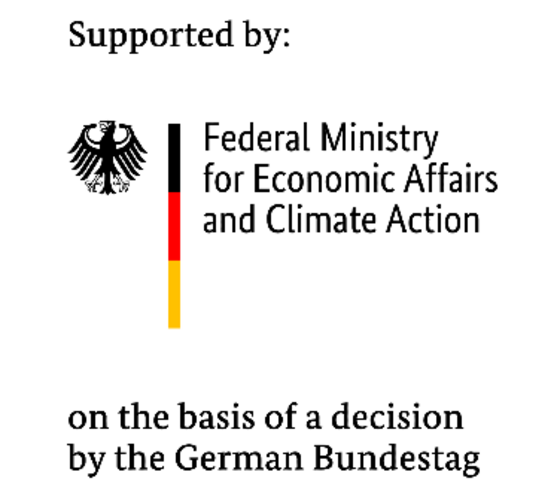
CFD modelling of a continuously flowing rotor-stator mixing system for Newtonian and non-Newtonian mixable high-viscosity substance systems
The mixing of high-viscous fluids is often a quality-decisive step that is widely used in plastic, chemical, pharmaceutical and food processing industries. As a result of the high viscosity, flows often remain in the laminar regime during the mixing process. Due to the lack of turbulence, rapid mixing down to the molecular level is thus technically challenging, specially, since both shear rate and power input cannot be freely selected (due to the desired product properties). Furthermore, often various components within a wide range of material parameters and with different mass flows have to be mixed, which further increases the complexity of the process.
Rotor-stator mixing systems are often used on an industrial scale to tackle the mixing task. The systems are characterized by a periodic arrangement of stationary and rotating blades in a cylindrical housing. Despite the outstanding performance comparing to the traditional mixers, determining the optimum operating parameters of a rotor-stator mixing system is both time-consuming and expensive and should be reduced in terms of time, experimental effort and personnel.
Computational fluid mechanics (CFD) is the great tool to tackle this problem, where different regimes and characteristics of the flow within a rotor-stator mixer could be efficiently discovered and categorized. The classical CFD methods, however, have two drawbacks:
- The pre-processing (i.e., mesh generation) and the modelling of the complex rotating components are normally time consuming and often numerically unstable. Most of the time, the consideration is limited to symmetrical conditions, so that asymmetrical influences of rotor-stator mixers are not considered in the simulation so far.
- The mixture of two fluids is normally modelled using transport equations. The numerical solution of these equations results in numerical diffusion due to grid quality and the discretization.
Too address these challenges, a simulation method is being developed at the Chair of Fluid Mechanics of the University of Wuppertal, which takes advantage of an Immersed-Boundary Method (IBM) as well as a Lagrangian approach. The in-house IBM code, ABSFoam, is being further developed and optimized for the application in rotating systems. ABSFoam offers the possibility to easily modify different rotor or stator geometries without extra effort on the mesh generation. Furthermore, asymmetric motion shapes (e.g., eccentricity) can be investigated easily in the model.
To accurately simulate the mixing process, a particle-based method (Lagrangian) for the prediction of the mixing quality in rotating systems in connection with the IBM is being developed as well. The aim is to find ways to describe the mixing behavior of media with different viscosities using particle-based methods. This Lagrangian approach is not numerically diffusive, as the phase distributions are calculated explicitly from the particle distribution, instead of solving a transport equation (Eulerian approach).